Using Continuous Offline Insulation Resistance Testing and CBM to increase Plant Safety and Reliability
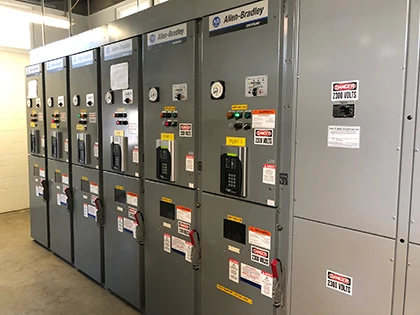
Since over 80% of electrical maintenance testing involves evaluating insulation integrity, the first and most important test done on electrical equipment is an Insulation Resistance (Meg) Test. This is because electrical insulation begins to age as soon as it’s manufactured and aging causes deterioration in the performance of the insulation. Harsh operating environments will also cause further deterioration, especially where the electrical insulation is exposed to extreme operating temperatures, moisture, and chemical contamination. As a result, personnel safety and operating reliability can both be compromised. It’s extremely critical to always know the electrical condition (IR) of the insulation in your equipment at all times.
For decades, plant personnel have had to perform periodic insulation resistance tests with handheld megohmmeters to prevent motor failures that lead to costly unplanned shutdowns, penalties and expensive re-winding repairs.
However, these tests only provide a “snapshot” of the motor’s health. In a matter of only a few days, motor windings and cables that are exposed to moisture, chemicals, contaminants or vibration can become compromised and fail at startup.
Portable megohmmeters also require electrical technicians to manually disconnect the equipment cables and connect the test leads on potentially energized or damaged equipment to perform the manual testing.
These tests expose technicians to potential arc flashes when they access the cabinet. In the United States non-fatal arc flash incidents occur approximately 5 to 10 times per day, with fatalities at the rate of approximately one per day.
With so much at risk, plant managers are recognizing the value of permanently installed continuous megohm testing and monitoring of insulation resistance that initiates the moment the motor is off until it is re-started again.
Armed with this real-time information, maintenance personnel are able to take corrective actions ahead of time to avoid a failure that would interrupt production. By doing so, they can save utilities hundreds of thousands of dollars in repair fees for expensive rewinding, failure-to-produce penalties and lost production time.
Furthermore, permanently installed automatic testing devices allow for “hands-off” monitoring without having to access cabinets – keeping technicians out of harm’s way.
Read full article in the Reliable Power Testing Special Edition 2021